COMMONLY ASKED QUESTIONS
- julie89561
- Jan 29
- 4 min read
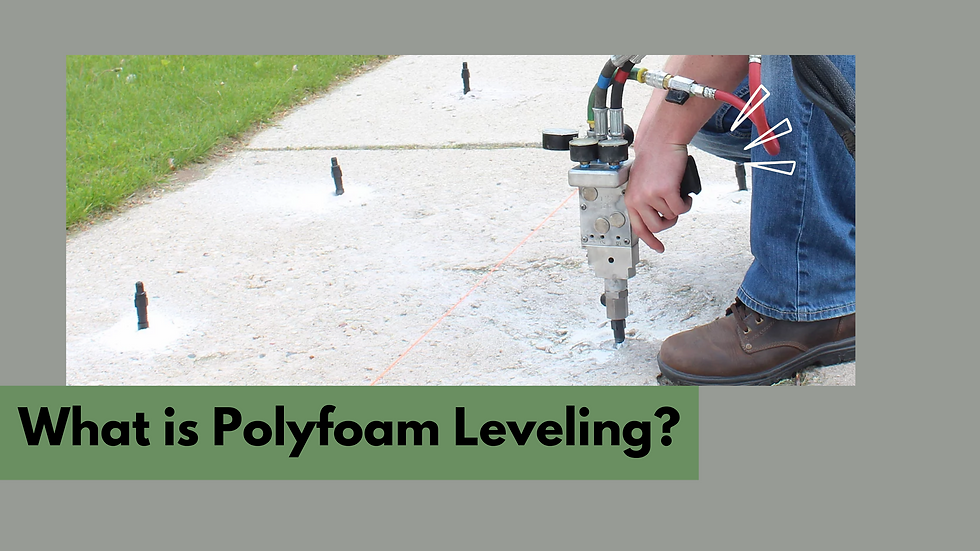
Polyfoam leveling typically refers to a process used in construction and building projects to create a level and stable surface. Polyfoam, short for polyurethane foam, is a material known for its lightweight and versatile properties. Here is a detailed explanation of polyfoam leveling:
1. Material: Polyurethane Foam
Composition: Polyurethane foam is a type of plastic that exists in various forms, including rigid and flexible. It is created by combining two main components - polyol and isocyanate - through a chemical reaction.
2. Purpose of Polyfoam Leveling:
Uneven Surfaces: Polyfoam leveling is primarily used to address uneven or sloping surfaces in construction projects. This could be floors, concrete slabs, or other surfaces that need to be raised to eliminate trip hazards, allow for flooring or materials to be installed, and fix/prevent water drainage issues.
3. Application Process:
Site Assessment: Before application, a thorough assessment of the site is conducted to identify areas that need leveling. This could involve measuring slopes and identifying low or high points.
Preparation: The surface is prepared by cleaning it thoroughly and ensuring that it is free from debris and contaminants.
Injection Points: Holes are drilled into the surface to inject expanding polyurethane foam. The size of the holes can vary depending on the specific product and application. In general, the holes are relatively small, often around five-eighths of an inch.
Injection of Polyurethane Foam: The polyurethane foam is injected into the designated areas through strategically placed injection points. The foam expands to fill voids and lift the sunken or uneven sections, creating a level surface.
Monitoring and Adjustments: During the process, the expansion of the foam is monitored, and adjustments may be made to ensure an even and controlled lift.
4. Advantages of Polyfoam Leveling:
Lightweight: Polyurethane foam is lightweight, reducing the overall load on the structure.
Quick Installation: The process is relatively quick compared to traditional methods of leveling.
Minimal Disruption: Polyfoam leveling causes minimal disruption to the existing structure and surroundings.
High Load-Bearing Capacity: The cured foam has a high load-bearing capacity, providing stability to the leveled surface.
5. Post-application:
Curing Time: The polyurethane foam requires some time to cure and harden fully. The curing time may vary depending on factors such as temperature and humidity.
Finishing: Once cured, the surface may be finished as needed, such as by applying flooring materials or other finishes.
6. Considerations and Limitations:
Professional Installation: Polyfoam leveling is performed by trained professionals to ensure proper application and results.
Compatibility: While suitable for many applications, it may not be suitable for all surfaces or conditions.
In summary, polyfoam leveling is a method that utilizes the expanding properties of polyurethane foam to level uneven surfaces in construction projects, providing a stable and durable foundation for further construction or finishing work.
Is Polyfoam Leveling Suitable for all Concrete Surfaces?
Polyfoam leveling is generally suitable for a variety of concrete surfaces, but its effectiveness can depend on the specific conditions and requirements of the project. Here are factors to consider when determining if polyfoam leveling is suitable for a particular concrete surface:
Type of Concrete:
Condition of the Concrete:
Load-Bearing Capacity:
Accessibility:
Moisture Content:
Environmental Considerations:
Professional Assessment:
While polyfoam leveling is a versatile and effective solution for many concrete leveling applications, it is not a one-size-fits-all approach. The suitability of polyfoam leveling depends on the unique characteristics and challenges of each project. Consulting with Elevation Concrete Raising & Repair can help determine the most appropriate solution for your specific needs
How long does the polyfoam leveling process take?
The duration of the polyfoam leveling process can vary based on several factors, including the size and complexity of the project, the type of polyurethane foam used, and the environmental conditions. Here is a detailed breakdown of the typical steps involved and the time it may take:
Site Assessment:
Preparation:
Drilling Holes:
Injection of Polyurethane Foam:
Curing Time:
Cleanup and Restoration:
Final Inspection:
Total Duration:
It is crucial to note that these time estimates are general guidelines, and the actual duration can vary based on the specific circumstances of each project.
What is Visible Once Polyfoam Leveling is Completed?
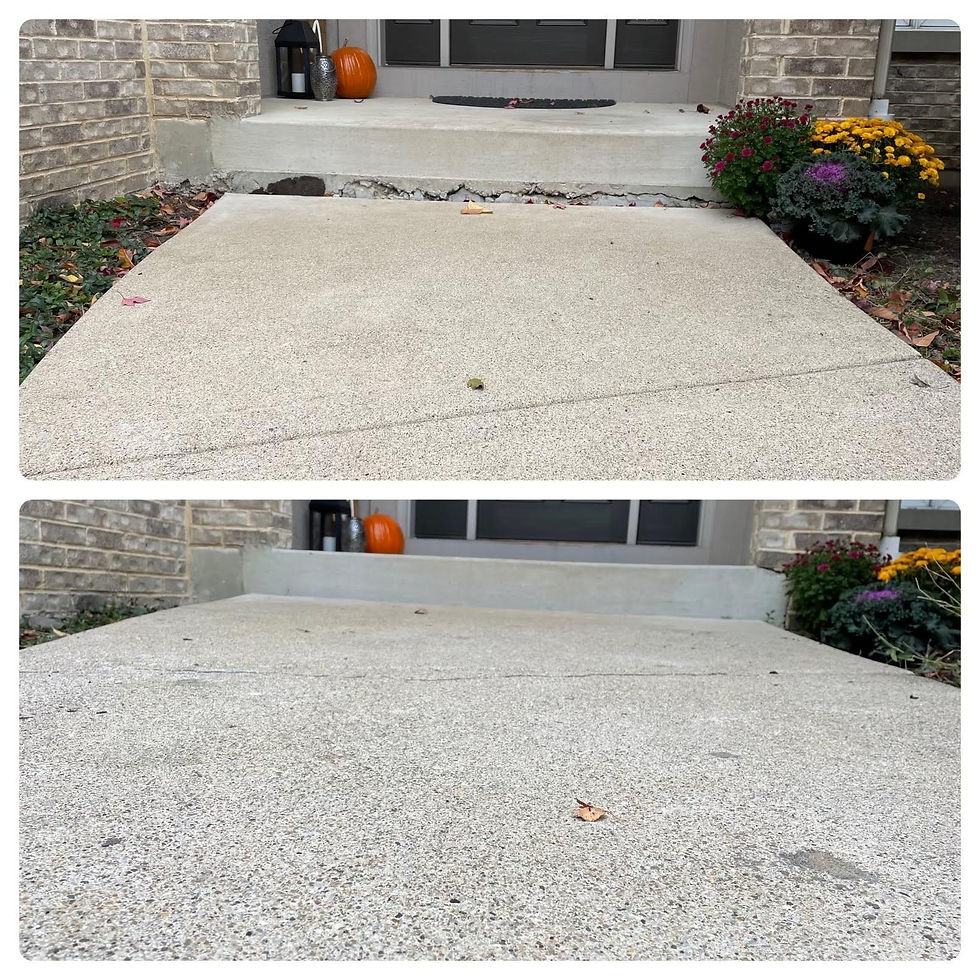
After polyfoam leveling is completed, the visibility of the work will depend on several factors, including the type of surface treated. Here is a detailed explanation of what may be visible after polyfoam leveling:
Patch Marks:
The drilled holes used for injecting polyurethane foam are typically patched or sealed after the process. These patches may be visible on the surface.
Trimmed Excess Foam:
Any excess foam that expands beyond the targeted area during the injection process will be trimmed and removed. Any exposed edges should be filled with soil by the property owner.
Overall Aesthetic:
In a well-executed polyfoam leveling project, the overall aesthetics of the treated area should be improved. Uneven surfaces should be leveled, resulting in a more uniform appearance.
Minimal Disruption:
One of the advantages of polyfoam leveling is its ability to minimize disruption to the surrounding area. Unlike traditional methods that may involve extensive excavation, polyfoam leveling leaves the surrounding landscape largely intact.
Tripping Risks are Eliminated:
By leveling the concrete surface and addressing the underlying settling issues, polyfoam leveling helps prevent future trip hazards. The stabilized and lifted concrete is less likely to settle unevenly in the future, reducing the risk of new trip hazards developing.
Final Inspection:
Before completing the project, a final inspection is typically conducted to ensure that the leveling is successful and the surface is restored to its desired level. Any visible issues or discrepancies are addressed during this stage.

Comments